Набор для сборки Delta 3d принтера с двумя hotend-ами
Снова приветствую всех. Полагаю, многим, кто интересуется 3D печатью будет интересен обзор принтера Delta Rostock mini G2s pro от от китайского производителя Geeetech. Это обновленный Delta Rostock mini G2s. Посмотрим насколько хорошо производитель сделал «работу над ошибками».По поводу п.18
После прошлых обзоров магазины обращались с предложениями обозреть всякую скучную (но возможно полезную) мелочь либо вещи, о которых мне нечего сказать. Я отказывался, мне скучно и лень этим заниматься только из-за пресловутой халявы. Покупки в Китае для меня — это очередное маленькое хобби, не связанное с особым желанием экономить. Поэтому я бессовестно предложил banggood-у дать на обзор этот набор, не особо рассчитывая на согласие. Магазин сказал, что это дорого и снова предложил обойтись дешевой вещью. Тогда я предложил разделить расходы пополам и магазин согласился. Но на всякий случай ставлю тег о п.18, для успокоения кипящих наших разумов возмущенных у отдельных товарищей. Для них же скажу, что мне глубоко наплевать на плюсы и минусы, я пишу только для увлеченных и интересующихся, а вожусь с китайскими товарами только для удовлетворения собственного любопытства и потому что я немного шопоголик 🙂 Поэтому недовольных и полных сарказма прошу — поставьте минус, закройте обзор и не парьтесь.
Итак, месяц проведя в рутине повседневности, я наконец получил заказанное добро. До этого я податамайнил, собрал информацию о производителе и его продукции, изучил опыт других приобретателей и приготовился к худшему. Дело в том, что со старой версией Geeetech (и так не имеющий ярко выраженной положительной репутации из-за качества комплектующих ранних моделей) явно облажался — некачественное литье деталей, непродуманные элементы конструкции, косяки исполнения электротехники и проч.). Народ плевался, но брал из-за цены и пилил, пилил… С «не фонтан» саппортом ситуация только ухудшалась. Производитель услышал чаяния народа и выпустил апгрейд с приставкой pro (кстати, комплект проапгрейженных деталей также продается отдельно).
Апгрейд свелся с замене пластиковых деталей на алюминиевые и устранению явных косяков, бросающихся в глаза. Буду описывать в хронологии сборки и делать акценты на изменения. В конце — сделаем вывод. Это будет «честный детектив», как говорил один ведущий с оттопыренной нижней губой.
Характеристики
Область печати: цилиндрическая, D: 170mm, H:200mm (этот показатель зависит от настроенной длины тяг)
Рама: акриловая, вырезанная лазером
Толщина слоя: от 0.1мм
Разрешение слоя: 0.1мм
Диаметр филамента: 1.75мм, 3мм
Диаметр сопла: 0.3,0.35,0.4,0.5 мм
Скорость печати: 60 до 120 мм/сек
Размер стола для печати: 210*3мм
Стол дял печати: алюминиевый + нагреватель (heatbed)
Максимальная температура hotend-а: ~240℃
Вход питания: 115V/2.2A или 230V/1.1A
Выход питания: DC12V/20A
Количество экструдеров/hotend-ов: 2
Интерфейсы: USB, SD Card
Материнская плата: GT2560
Автовырвнивание: есть
Габариты собранного принтера: 320*320*870мм
Вес собранного принтера: ~10кг
Габариты упаковки: 495*395*195мм
Вес с упаковкой: 11кг
Итак, груз прибыл в картонной коробке весом около 10 кг. Внутри коробки в лотке из вспененного поли… эээ… мерного материала по отдельчикам были аккуратно в пронумерованных пакетиках разложены детали с приложенной спецификацией. Фото я не делал, поэтому приведу заимствованные с сайта одного из мучеников старой версии robstechtank.com:
Первое впечатление — положительное. Все аккуратно, систематизировано, идентифицируется со спецификацией. Поскольку я покурил к этому времени мануал по сборке, то все хозяйство вываливать на стол и любоваться не стал, а сразу начал сборку с творческими перерывами на модернизации и отдых…
О дельтах
Кинематика дельты крайне чувствительна к любым погрешностям механики. В этом мы убедимся. Вместе с тем, работающая дельта завораживает как огонь, текущая вода и чужая работа. И стол не елозит туда-сюда 🙂Настройка дельты — танцы с бубнами, любой Mendel-подобный принтер в этом плане по сравнению с дельтой — ягненок. Вместе с тем дельта по многим косякам исправляется конфигурированием прошивки, чего не скажешь о менделях с окончательно и бесповоротно кривыми валами и вобблингом шпилек (это всё моё IMHO).
Отдельное слово о двуэкструдерных дельтах — это гемор почище «Фауста» Гёте. Один хотенд настроить еще можно, а два — нужно идеальное исполнение механики с точностью до сотых миллиметра. Отсюда всякие хитрые решения типа механически управляемого выбора хотенда или хотенд-циклоп. Тем не менее иногда получается настроить достаточно качественно и без извращений, о чем будет речь ниже.
Итак, вернемся с нашему персонажу. Платформы (верхняя и нижняя) — из акрила. В последнее время это популярный у китайцев материал для рам принтеров. Красив, притягивает пыль, крайне хрупок при сборке. Зато красиво режется лазером.
Рама собиралась без проблем, прошлые косяки с размерами посадочных отверстий устранены, за исключением отверстий под панель управления и держателей катушек с филаментом. Решается все дремелем за минуту.
Собираем нижнюю платформу, которая содержит в себе шаговые двигатели, материнскую плату, LCD-экранчик. Сверху на платформу прикручивается подпружиненный стол с нагревателем (т.н. heat bed):
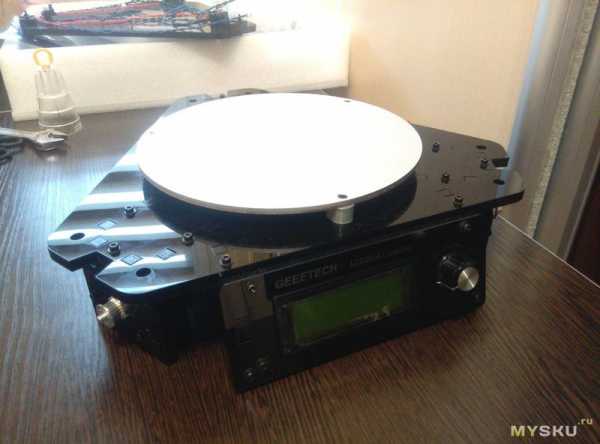
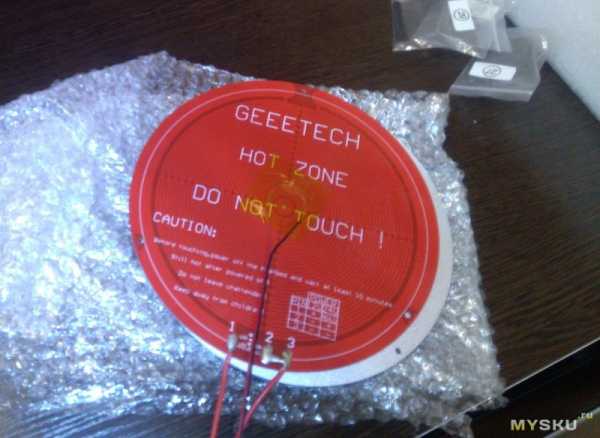
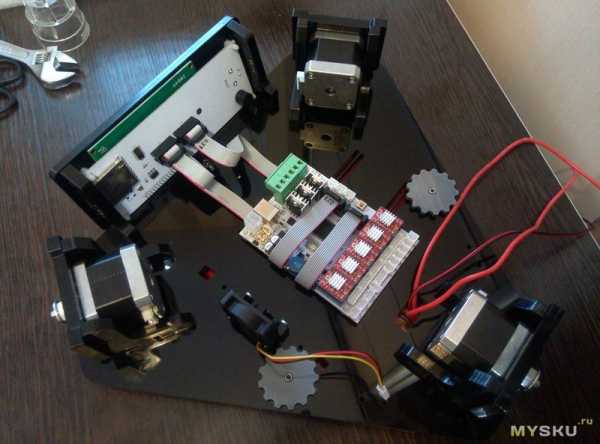
Могу отметить, что производитель пофиксил недостаток прошлой модели — непропайку секций нагревателя, что приводило к тому, что он грелся наполовину от своей возможности.
Обратите внимание на серые колеса — это я распечатал вместо штатных «барашков» для более легкого выравнивания heat bed. Принтер имеет систему автокомпенсации наклона, т.н. autoleveling, но я как-то привык вручную.
Обязательно под шайбы, прилегающие к нагревателю стола подкладывайте изоляторы (или используйте неметаллические шайбы). Я пренебрег этим, чуточку повредил шайбой защитный слой — и нагреватель замкнуло по алюминиевому столу, через винты которым нагреватель притянут к столу. Будьте осторожны, в результате, при попытке нагрева стола — может выйти из строя соответствующий mosfet-транзистор.
Собираем каретки:
Потом собираем «паука» — эффектор с hotend-ами и тягами. Сперва выравниваем расстояния между центрами подшипников тяг. Это сделать не так просто, т.к. все резьбы фабрично залиты красным локтайтом. Но накалив наконечники горелкой, потихоньку отворачиваем. После этого делаем шаблон, используя штатные штоки (на «кроватки» для наконечников не обращайте внимания, это исключительно мое личное извращение. достаточно просто просверлить в доске отверстия для штоков)
Потом все тяги выравниваем по шаблону, подкручивая наконечники на нужное расстояние.
Второй раз локтайтом, даже синим, я резьбы не фиксировал, а лишь уплотнил их фум-лентой. Скажу сразу, что идея производителя с алюминиевыми тягами и локтайтом мне не очень понравилась, возможно заменю позже на легкие углепластиковые вместе с эффектором на магнитных шарнирах. К слову, штатные наконечники имеют местами заводской люфт подшипников — для компенсации надевают резинки либо напечатанные стяжки.
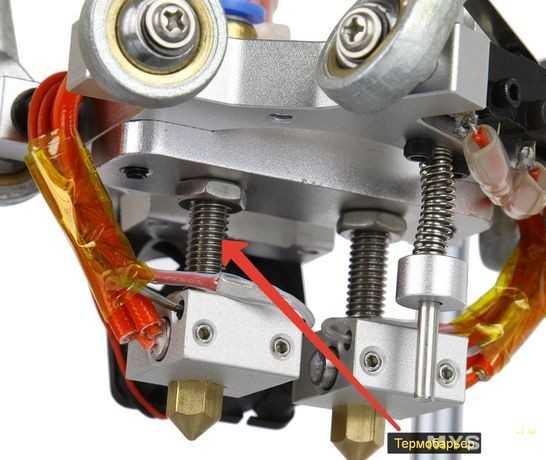
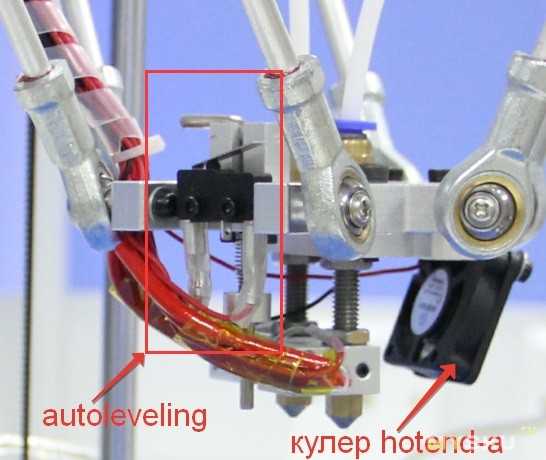
я, оставив механизм autoleveling, решил изменить, т.к. ненаправленный обдув термобарьеров маленьким кулером по идее рано или поздно должно влечь «непроходимость» филамента, а отсутствие хоть какого-нибудь обдува пластика на выходе — косяки при печати пластиком PLA.
Поэтому, вооружившись штангециркулем, я на скорую руку сделал твердотельную модель новой конструкции в Solid Works:
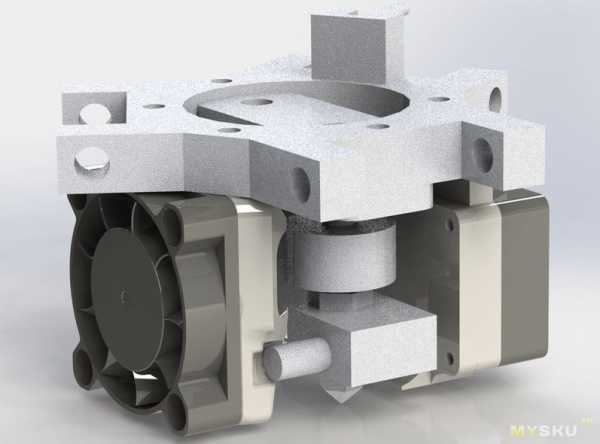
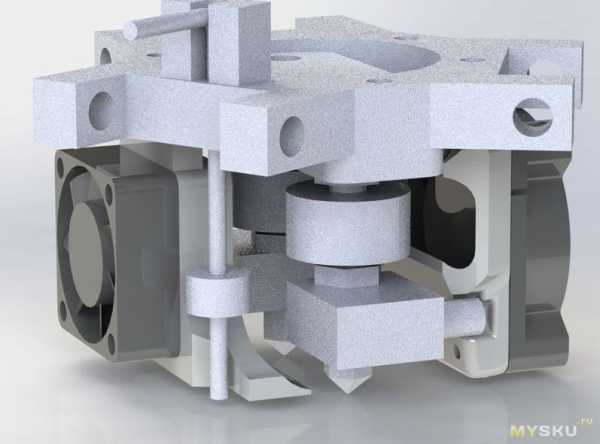
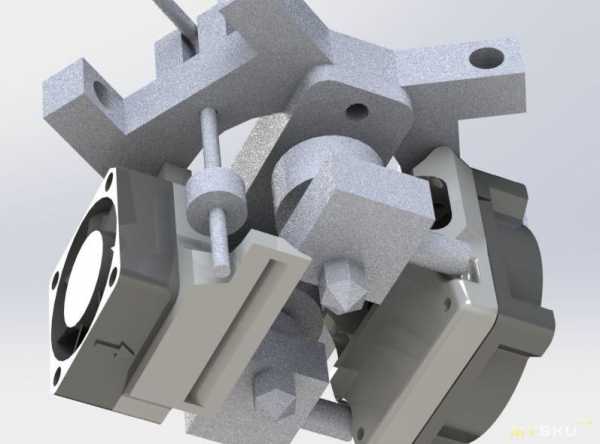
Распечатав на втором принтере несколько вариантов воздуховодов-
я полностью перебрал hotend, установив при помощи термоклея радиаторы на термобарьеры, герметизировал все резьбы, изменил ориентацию проводки, закрепил термисторы при помощи термопасты и термоклея (они болтались внутри нагревателей, имелся воздушный зазор). При помощи штангенциркуля выставил сопла hotend-ов:
Собираем «паука» целиком:
При сборке выяснилось что штоки для подшипников слишком длинные, чтобы подшипники не «болтались». «Болтанию» также способствуют фаски на отверстиях подшипников (т.е. утолщение штока «проваливается» вглубь подшипника на ширину фаски). Выход — либо укоротить штоки, либо поставить шайбы на штоки. Я лично сперва поставил шайбы, но они оказались слишком мягкими (я их напечатал). Поэтому либо купить жесткие шайбы с наружным диаметром, который не будет мешать подшипнику, либо (как это сделал я), укоротить штоки и нарастить утолщения штоков (я это сделал каптоном шириной 4мм)
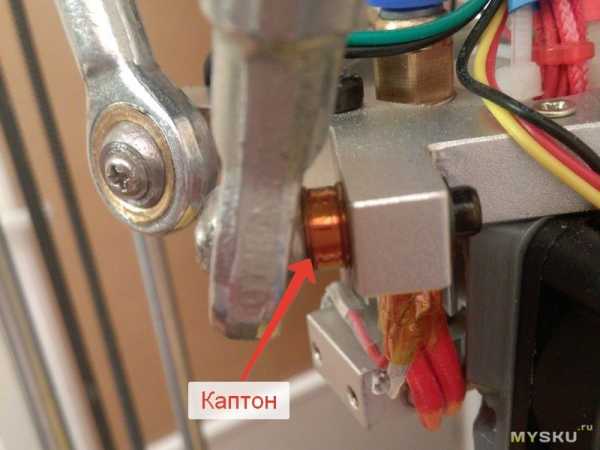
Устанавливаем направляющие (вместо шайб под винты их креплений на нижней платформе я подложил уголки из детского конструктора, что бы иметь большую площадь приложения силы), на них одеваем каретки, потом крепим верхнюю платформу. Отмеряем, нарезаем ремни и закрепляем их на каретках:
Затем при помощи роликов натягиваем из закрепляем ремни:
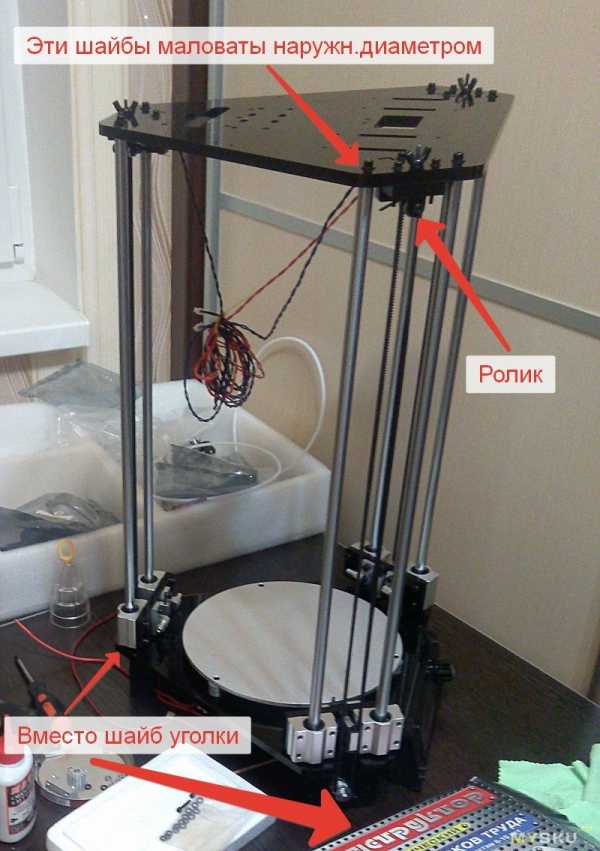
Вот тут выяснилось, что подшипники роликов хлипкие и я заменил все ролики парами подшипников f624zz, практически идеально для этого подходящими:
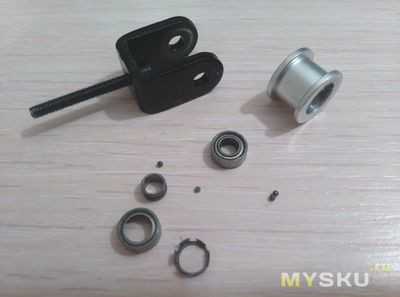
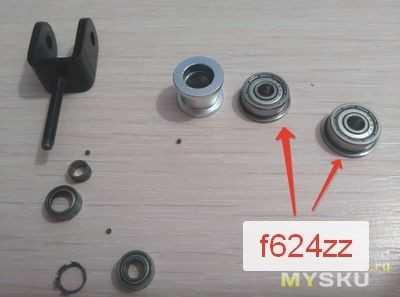
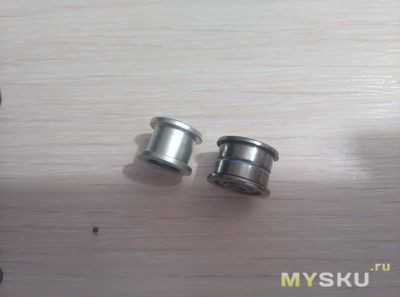
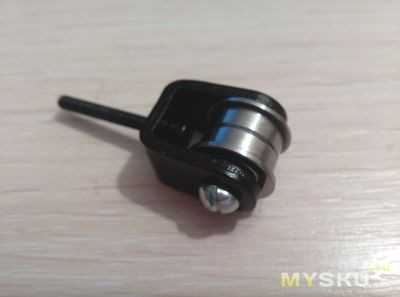
Устанавливаем экструдеры, предварительно сняв с них кулеры (им практически нечего охлаждать, я их использовал для установки на термобарьеры и дополнительного обдува материнской платы):
Направляюще для филамента можно взять отсюда.
Наконец устанавливаем паука на каретки, упаковываем проводку в бандаж и валим принтер набок — для подключения проводки к материнской плате:
Наконец устанавливаем держатели катушек с филаментом, облагораживаем блок питания (я распечатал ему простые элементы корпуса), соединяем экструдеры с hotend-ами трубками и заправляем в экструдеры филамент:
Обращаю внимание на синий держатель на фото. Это маленькая штучка предназначена для того, что бы справится с тем, из-за чего народ меняет материал тяг или эффектора. Дело в том, что эффектор с тягами достаточно тяжел, что бы, после окончания печати и отключения шаговых двигателей, съехать прямо на модель. Можно, конечно этого избежать, заблокировав в прошивке отключение моторов после печати, но можно также распечатать такой маленький держатель, который вставляется после начала печати, самой печати не мешает, а после парковки головки в конце печати, удерживает одну из кареток после отключения двигателей.
Что касается подключения кулеров- ни в коем случае не подключайте обдув терьмобарьера к ШИМ разъему по инструкции. Это явная недодумка производителя. К этому разъему, как правило подключается, обдув филамента на выходе, в то время как обдув термобарьера должен работать непрерывно. С учетом демонтажа кулеров с экструдеров, у вас не будет проблем с поиском свободного разъема на материнской плате.
Наконец, вносим нужные изменения в конфигурацию прошивки, калибруем принтер (это предмет отдельного разговора), добавляем боросиликатное стекло (я его купил отдельно, что необязательно), на которое наклеен каптон, и пробуем делать пробную печать.
Получилось! Теперь можно продолжить шаманить с профильным софтом и заниматься улучшениями. Тонкая настройка дельты — это также предмет отдельного разговора. Достаточно сказать, что я даже сделал в SW кинематическую модель дельты, что бы изучить степень влияния механических погрешностей на поведение принтера. На этой модели я и выяснил, что нужно поправить/подкрутить, чтобы избавится от недостатков печати.
Так, например, обнаружив, что уровень сопел относительно друг друга меняется на противоположный от одного края платформы к центру и другому краю, я с помощью модели выяснил, что причина — в разные расстояниях между соседними наконечниками парных тяг. Но это уже танцы с бубнами, которые сопровождают любого, кто проходит путь самостоятельной сборки и эксплуатации 3d принтера.
Резюме:
1. Аппргейд сыграл неоднозначную роль. С одной стороны — избавились от большинства косяков (плохой пластик, плохие инструкции, дефекты электротехники и лазерной резки рамы), но металлические части утяжелили конструкцию, что повлекло необходимость фиксации «паука» после печати.
2. Плохие подшипники роликов — рекомендую сразу на замену по моему варианту.
3. Необходимость «юстировки» тяг — заводская юстировка оставляет желать лучшего.
4. Концевые выключатели лучше припаять, т.к. терминалы ломаются при сгибе, требуемом по инструкции.
5. Достаточно тяжело выравнивать уровень сопел hotend-ов относительно стола.
6. Отсутствие радиаторов на термобарьере смущает, как и целом конструкция двойного hotend-а. Однако конструкция работает.
7. Электроника, двигатели, линейные подшипники кареток, направляющие валы, т.е. все самое важное — порадовали, без косяков
Вывод: Комплект хороший, но явно не предназначен для сборки и использования аля «plug-and-play», как, в прочем и любой набор для сборки 3d принтера. Два hotend-а и дельта-кинематика делает сборку еще более геморройной и увлекательной. Но если справитесь — дельта порадует вас. Для начинающих я бы рекомендовал версию этой же дельты с одним экструдером и hotend-ом — это будет и дешевле и проще в сборке и настройке. В магазине этот набор есть.
Видео
ЗЫ. Ах да, забыл сказать про автоуровень — я его так и не использовал, т.к. настроил все при сборке и калибровке так, что он мне стал (м.б. пока) не нужен. Но он подает признаки работы — я проверял 🙂
Huxley не рад конкуренту 🙂
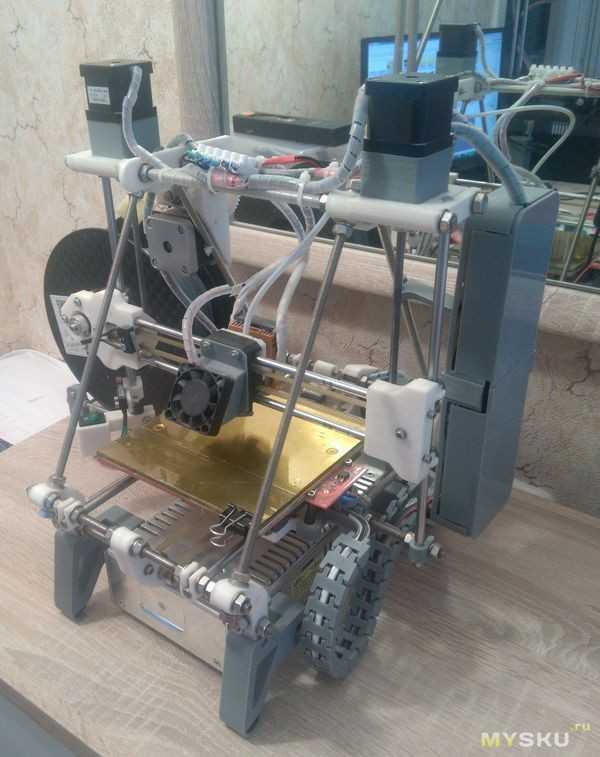
Товар предоставлен для написания обзора магазином. Обзор опубликован в соответствии с п.18 Правил сайта.
mysku.ru
Собираем дельта 3D-принтер своими руками
Появление 3D-принтера ознаменовало революцию в сфере технологий. Оборудование нашло широкое применение и в бытовых условиях, и на производстве. Однако, объёмную печать пока что сложно назвать доступной технологией. Чтобы разобраться в ней и сэкономить на покупке оборудования, можно собрать дельта 3D принтер своими руками. Для этого нужно правильно выбрать рекомендуемые запчасти и в точности соблюдать указанную последовательность действий.
Основные преимущества дельта принтера
Ранее мы уже рассказывали, какими отличиями обладает delta 3D принтер. Если же говорить о том, что выбрать лучше, дельта 3D принтер или обычное оборудование, сначала отметим его основные преимущества:
- Высокая точность изготовления даже мелких и тонких деталей;
- Простота перехода на другие экструдеры;
- Зрелищный рабочий процесс.
Помимо того, принципиально новая схема сборки позволяет оборудованию быстрее печатать более высокие и сложные предметы, чем это делает большая часть аналогичных принтеров.
Каковы главные недостатки дельта принтера
Как и другие новинки технологического рынка, такие принтеры имеют ряд недостатков:
- При печати моделей с большим количеством точных деталей на высоких скоростях возникают сложности с расчетами;
- Калибровка delta 3D принтера сложнее, чем у «обычного» оборудования для объёмной печати;
- Принтер обладает сложной конструкцией, что особенно важно при самостоятельной сборке.
Конечно, важным недостатком является и дороговизна оборудования, но это не должно вас беспокоить, если всю работу вы собираетесь сделать сами.
Реально ли собрать самодельный дельта принтер
Первый собранный своими руками принтер такого типа появился именно из-за высоких цен на «готовое» оборудование, реализуемое поставщиками. Решив сэкономить, американский изобретатель задался целью сделать дельта принтер самостоятельно. После череды попыток он достиг успеха и доказан, что воссоздать это революционное для всей индустрии объёмной печати оборудование можно самому. При этом бюджет в таком случае можно сократить в несколько раз.
Выбор необходимых деталей
Подбор запчастей — самый ответственный момент. Успешно справившись с ним, при должном усердии собрать дельта 3D принтер своими руками получится у каждого. Чтобы собрать работоспособный аналог дорогостоящего оборудования, вам понадобится запастись:
- крепкой рамой;
- направляющими валиками;
- резьбовыми шпильками формата M5;
- платой расширения RAMPS 1.4;
- Arduino Mega 2560 R3;
- понижающим регулятором напряжения;
- комплектом моторов шаговых;
- механическими ограничителями.
Дополнительно понадобится дисплей, а также блок питания 12В и кнопка с клеммой 220В. Также потребуется экструдер, кулер для обдува деталей и ещё один кулер, чтобы обдувать драйвера. Наконец, не забудьте обзавестись горячим столом, позволяющим работать с PLA и другими материалами.
Как выполняется постройка дельта принтера
Сборка оборудования начинается с крепления рамы и торцевых опор. Ходовые винты нужно оставить свободными вверху. Пластиковые втулки, идущие совместно с рамой, следует использовать по назначению.
Бесперебойная работа техники будет возможна, если отвязать Arduino от питания, выпаяв или отрезав диод с платы RAMPS. Затем регулятор напряжения нужно припаять ко входу питания. Попутно с этим нужно выпаять стандартное гнездо питания, после чего приклеить регулятор сзади Arduino.
Питание от блока к RAMPS спаивается отдельно к ножкам, после чего укладываются все провода. Ограничители важно установить в направлении правильной полярности.
ubibbl.com
«Дельта» 3D-принтер, как альтернатива стандартному оборудованию
Классические настольные 3D-принтеры построены по принципу Декартовой системы координат. То есть, печатная головка двигается сугубо по осям X, Y и Z. Немногие знают, что помимо привычных FDM-аппаратов на рынке устройств для трехмерной печати регулярно появляются принципиально новые «дельта» 3D-принтеры. В отличие от привычных нам XYZ-принтеров, они используют принципиально новую схему работы экструдера: печатная головка подвешивается на тонких рычагах, каждый из которых крепится к одной из трех вертикальных направляющих. Такая конструкция позволяет печатать более высокие и сложные фигуры.
Дизайнер Мэтт Уолерс серьезно занялся разработкой дельта-принтеров. После чреды провальных в коммерческом плане проектов, инженер-аматор таки нашел золотую середину – дельта-принтер собственной разработки Thingystock. В основе устройства лежит конструкция RepRap-принтера Rostock. Другими словами, больше половины запчастей печатного аппарата могут быть воссозданы в домашних условиях. Изобретатель считает, что такой подход обязательно понравится пользователям.
3D-принтер Thingystock оборудован экструдером E3D V6. Рабочая камера позволят печатать модели, соответствующие габаритной формуле 150 х 150 х 150. Управление рабочим процессом осуществляется при помощи встроенного процессора RAMPS 1.4. Коррективы и настройки вводятся при помощи ЖК-дисплея. Точность печати составляет 150 микрон. Казалось бы, ничего необычного. Но Мэтт Уолерс с этим не согласен. Оказывается, ременные шкивы, крепления экструдера и направляющие подлежат замене, благодаря чему можно заметно повысить качество печати, а также увеличить объем камеры построения. При этом цена устройства не превышает 550 долларов!
Если вы хотите получить в собственное распоряжение профессиональный дельта-принтер, тогда вам следует детальнее ознакомиться с предложением китайской компании Atom. Китайские инженеры уверяют, что их детище под названием Atom 2.0 претендует на звание лучшего из ныне доступных настольных дельта 3D-принтеров. Стоит отметить, что громкие заявления инженеров недалеки от истины.
Если большинство дельта-принтеров не могут похвастаться надежностью сборки и точностью печати, то об Atom 2.0 такого не скажешь. Все узлы аддитивного устройства изготовлены из металла. Модульная конструкция дополнительно укомплектована тремя вентиляторами: один обслуживает экструдер, а два других обдувают напечатанные объекты для того чтобы ускорить процесс затвердевания пластика. Отдельно стоит упомянуть инновационную систему автоматического натяжения ремней, заметно повышающую качество печатного процесса. Стоит китайский «атом» чуть больше $1500.
make-3d.ru
Сборка и печать деталей принтера Rostock. Часть 1
Ричард Хорн, вероятно, более известный многим как RichRap (через его очень популярный сайт, Twitter, Blogger и т.д.), описывает себя как «инженер в душе со страстью к тому, чтобы вещи работали в реальном мире». Его страсть к работе с 3D печатью, в частности, со всем, связанным с RepRap движением/культурой, феноменальна и неутомима. Его понимание реальности в сочетании с врожденной позитивностью делает его тем, на кого можно полностью положится и тем, кто всегда готов помочь с поддержкой людей которые имеют дело с 3D принтерами, независимо от того являются ли они ветеранами или новичками в этом. Ричард согласился опубликовать свои опыты со своим 3D принтером Росток на 3DPI. Как вы увидите, это было довольно интересное занятие, но некоторые результаты действительно потрясающие…
Итак, начнем со сборки Росток, документирование которой заняло некоторое время.
3D Принтер Росток изначально был разработан Иоганном C. Рочоллом и в настоящее время достаточно хорошо зарекомендовал себя в рамках RepRap. Прошло более года, и разработка имела много сопутствующих результатов и вариантов, сделанных другими пользователями и разработчиками. Даже у Иоганна есть новая модель (Kossel Wiki), основанная на алюминиевой конструкции с открытым верхом.
Мне очень нравилась простота оригинальной модели, и пока я думал о том, чтобы сделать алюминиевую Т-образную модель, где-то в это время SeeMeCNC делали их очень впечатляющую разработку, я остановился только на нескольких небольших изменениях для моей сборки Росток.
Росток имеет дельта / полярную конфигурацию, а не более распространенную декартовую систему координат, используемую большинством других RepRap. Основное отличие с дельта системой это то, что движение по вертикальной оси Z достигается за счет движения всех трех позиционных двигателей вместе, это связано с тем, что они находятся в треугольной конфигурации.
Основным недостатком является то, что вам нужна будет вертикальная область печати в два раза высше самой машины в связи с тем, что все нажимные стержни должны перемещаться вертикально до положения сопла в X и Y направлениях.
Механические настройки выглядят сложными, но в Ростоке меньше компонентов, чем в «нормальных» RepRap принтерах.
Это очень эффективная и компактная система позиционирования, которая использует только три двигателя, все имеют возможность двигаться с высокой скоростью с помощью ремней или даже лески «Спектра».
Обзорное видео Росток и комментарии, касающиеся сборки:
Сперва распечатайте набор пластиковых деталей с Johann’s Github Archive.
Универсальные шарниры немного сложные для печати, но их можно сделать 0,5 мм соплом, но лучше, если они напечатаны 0,4 мм соплом.
Шарнирные головки сделаны так, что в них вставляются либо углеродное стекловолокно, либо алюминиевая трубка, либо деревянные стержни. Я остановил свой выбор на дюбелях, сделанных из твердой породы древесины, приклеенных на место. Убедитесь, что все они одинаковой длины.
Как и в большинстве машин RepRap многие из ключевых деталей 3D печатные. Шарнирные головки могут быть полностью напечатаны.
Главные шарниры каретки и универсальные шарниры соединяются с использованием M3 болтов, шайб и гаек (спрятанных внутри каждой шарнирной руки).
Они должны быть плотно посажены, но, все же, свободно двигаться, не вращаясь.
Шарниры каретки присоединены – я использовал термозащиту от инфракрасного излучения на шарнирных головках, чтобы они хорошо держались.
Вам понадобится три вертикальных шарниров каретки, к ним нужно 2 х 8 мм (LM8UU) линейных опор качения и изолирующие втулки.
Линейные опоры качения очень шумные на этом принтере (я использовал именно их). Я бы настоятельно рекомендовал подумать об использовании печатных PLA / нейлоновых втулок или любого другого типа латуни, или пластиковых втулок вместо линейных опор качения.
В следующий раз, когда я буду разбирать этот принтер, я собираюсь заменить LM8UU этими нейлоновыми 618, напечатанными в Propsfactory.
Вам просто нужно, чтобы был небольшой зазор на вертикальных концах каретки. Вам может понадобиться использовать достаточно тонкие соединения с односторонним зигзагообразным расположением выводов для LM8UU/ изолирующих втулок или они будут задевать шарниры.
Затем доделанная каретка прикрепляется к изолирующим втулкам /LM8uu с соединениями с односторонним зигзагообразным расположением выводов.
Вам также понадобится немного 12мм фанеры или подобного материала для основы, и вы можете использовать то же самый материал для верхушки, я использовал 6мм прозрачные поликарбонатные листы так, как я буду добавлять твердость в дальнейшем с помощью алюминиевого Т-образного слота.
Одно из моих небольших изменений было добавление ножек этому принтеру. Они служат для того, чтобы поднять платформу так, чтобы можно было аккуратно установить электронику и блок питания под листом платформы. Также это обеспечивает устойчивую основу.
Можно присоединить двигатели Nema 17, а также можно добавить дополнительную опору подшипника, если вы хотите.
Я установил опору подшипника так, как я первоначально намеревался сделать с принтером линии Spectra. Свободная линия Спектра – простая латунная втулка и два напечатанных кольца.
У меня заработала вся каретка Росток с линией Spectra, но мне не нравились двигатели, они были недостаточной мощности и униполярного типа, так что теперь я решил использовать обратно обычные 2,5 мм ремни.
В первоначальной модели Росток, больше 12мм фанерных панелей было использовано для опорной стойки, я заменил их на легкие 20мм х 40мм прессованные алюминиевые (высотой 800мм) панели.
Использование алюминиевых участков позволяет легко прикрепить экструдеры, катушки и другие детали к машине и придает ей опрятный вид по сравнению с листами фанеры.
ЭлектроникаЯ придерживаюсь своей немного нетрадиционной 5-етапной системы крепления мест для нагревательных приборов, это способ мне подходит. Я добавил ПЭТ ленту для изоляции и для дальнейшей защиты отслеживания печатной платы. Сплошные медные стороны будут использоваться для печатной поверхности.
Приготовьте сетку в качестве изолятора, алюминиевую фольгу и карту в качестве теплозащиты/ рефлектора.
Проложите электрические провода и термистор, затем прикрепите их к фанерной платформе установочной шайбой, как это требуется.
>Я использую Arduino Mega и плату RAMPS 1,4 для этой сборки, это последняя, что у меня есть, так что платы RUMBA или Megatronics будут использоваться для будущих проектов…
Три датчика Холла устанавливаются на вершинах каждой оси, они идеальны для машины, такой как Росток, как исходное положение до самого верха. При печати головка движется вниз к печатной поверхности. Датчики на эффекте Холла используют маленькие магниты, которые находятся на каретке. Чтобы включить, вы можете настроить их встроенным потенциометром, так получается микровысокая точность первого слоя, и они отлично определяют положение повторно.
Вся электроника и блок питания смонтированы на вырезанной пластиковой доске для удобства сборки. Я использую 20A 12В питание. Всё подключено и по-прежнему легкодоступно (на всякий случай).
Продолжение сборки смотреть здесь.
www.3dindustry.ru
Рельса MGN9 для 3D принтера или мысли как собрать дельтабота
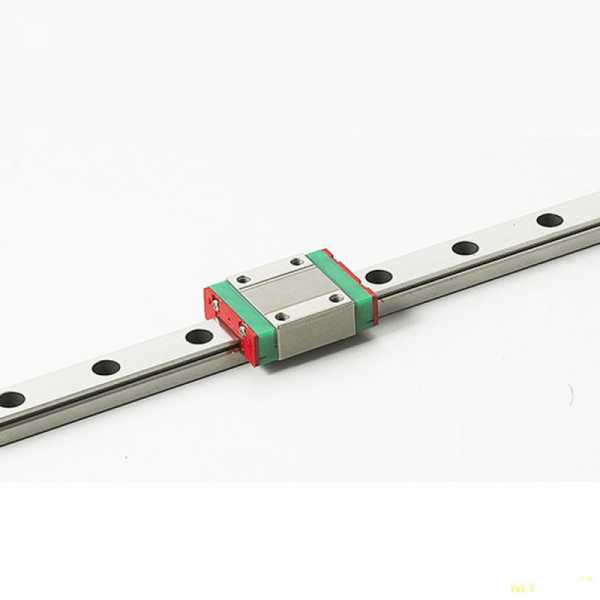
- Цена: Стоимость рельсы $15.69. Принтер обойдется примерно в $200+
Краткий обзор комплектующих для самостоятельной сборки 3D дельта принтера
В прошлом обзоре комплектующих для 3D принтера указали на отличие дельтабота. Я считаю, что несправедливо будет обойти вниманием 3D принтер подобной конструкции, поэтому вот небольшой список комплектующих и краткие инструкции для самостоятельной постройки дельта принтера.
Мой сегодняшний пост не является руководством к действию, а скорее затравочной информацией для обсуждения технических нюансов по созданию дельтабота.
У меня уже есть часть комплектующих и я потихоньку приступил с печати некоторых пластиковых узлов, остальные заказал в китайском магазине.
Для того, чтобы можно было повторить сборку самодельного 3D дельта принтера, привожу список запчастей для сборки. Указываю ссылки на бангууде, так как сам там брал одним большим лотом. Тоже самое есть и на Али, можно найти цены выгоднее, но тогда будет много-много мелких посылок. Смотрите сами, кому как удобнее.
Итак, для начала необходимо определиться об основных характеристиках будущего принтера. В первую очередь, это размеры принтера и печатной зоны. Обычно это круг диаметром 180…200 мм и высота 250….300 мм. От этих размеров уже и надо отталкиваться. В классическом Kossel размеры профиля 2020: 240 мм (9 шт. отрезков) и 680 мм (3 шт отрезка).
Информация по профилю
Информация про Соберизавод, как сделать заказ, и про скидку есть в этом обзоре.Режем 9 отрезков по 240 мм, 3 по 680 мм. Это стандартный Kossel. Для версий мини, XL и других размеры нужно пересчитать.
Вот скрин заказа
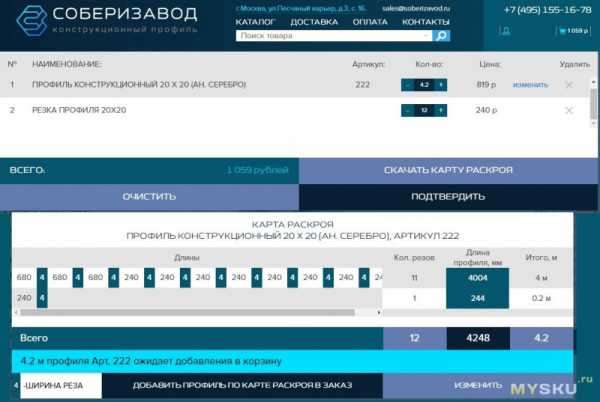
1059р самовывозом.
Далее определиться с типом перемещения: ролики по профилю или рельсы.
Ролики для профиля. Нужн
mysku.me
Преимущества и недостатки дельта 3D-принтеров
Среди различных конструкций 3D-принтеров наиболее удачной считается система «дельта». Ее кинематика имеет ряд преимуществ перед классическими 3D-принтерами с декартовой системой координат. Кроме того, дельта-принтеры выглядят интересно, а процесс их работы просто завораживает.
Проблемы декартовых 3D-принтеров и превосходство дельты
80% всех принтеров являются декартовыми. У них оси перемещения независимы друг от друга. Каждая отвечает только за свой вектор перемещения, просчеты для одной оси никак не могут повлиять на перемещение других.
Проблема декартовых принтеров заключается в слишком долгом перемещении из точки А в точку Б. Много времени уходит на разгон и торможение системы, прежде чем печатающая головка достигнет своей позиции. В итоге печать одной детали вместо двух часов может затянуться на четыре.
Конечно, можно повысить скорость перемещения, уменьшить время разгона и торможение, разогнав шаговые двигатели до более высоких скоростей и подкорректировав настройки в прошивке. Но электроника может не справиться с поставленной задачей, да и к тому же физику никто не отменял: детали головки слишком тяжелые, чтобы их вовремя ускорить или затормозить на больших скоростях, и поэтому головка просто не сможет резко разогнаться или вовремя остановиться. У двигателей появится пропуск шагов, это неизбежно приведет к смещению слоев детали.
У дельта-принтеров такая проблема отсутствует вовсе. При небольшой скорости двигателя головка движется максимально быстро за счет уникальной системы тяг. С такой конструкцией принтер производит печать на сверхскоростях, при этом затрачивает гораздо меньше усилий на перемещение печатающей головки.
Подводные камни дельта-принтеров
Оси перемещения у дельта 3D-принтера зависимы друг от друга. Небольшое изменение одной оси ведет к перемещению печатающей головки по всем трем координатам. Чтобы передвинуть головку хотя бы в одну сторону, нужно сделать расчеты по сложной формуле, которая должна учитывать всю конструкцию принтера, рабочую поверхность, длину тяг, габариты самого устройства и люфты.
Если вы решили собрать дельта 3D-принтер своими руками, готовьтесь к тому, что калибровка займет недели. Недостаток именно в настройке, так как малейший люфт или отклонение в геометрии конструкции вызовет серьезные искажения детали при печати.
Еще один недостаток дельты — это его габариты в высоту. Кроме выделенной области под печать часть объема принтера нужна для перемещения самой головки.
Немного слов об электронике Delta 3D-принтера
Поскольку дельта-принтер производит расчеты по сложным формулам, при его сборке вам придется побеспокоиться о хорошем контроллере. Для такого принтера желательно иметь 32-битную плату. Если взять обычную 8-битную, могут возникнуть проблемы при перемещении на длинные расстояния. Ресурсов вычисления будет катастрофически не хватать, и головка будет двигаться не по прямому, а по дугообразному пути. Помимо того, стоит побеспокоиться о точной калибровке дельта 3D-принтера — о том, как её выполнить, мы уже рассказывали ранее.
Несмотря на все недостатки, конструкция дельты считается наиболее удачной. Если правильно сделать геометрию, свести до минимума люфты и поставить хорошую электронику, вы будете радоваться своему самодельному принтеру очень долго.
ubibbl.com
Убираем боуденовскую трубку у «дельты»
Большинство моих статей написаны чисто ради графоманства. Но сегодня я преследую совсем другую цель. Возможно, кто-то вдохновится этим текстом и сделает систему, которая будет лучше той, которую я собираюсь описать. Потом он выложит свои результаты, а я — ими нахально воспользуюсь. Правда, нужны не идеи, а готовые STL файлы. Идей у меня у самого — полна голова, но истрачено уже столько времени и пластика на прототипы, что продолжать ни я, ни мой товарищ уже не в состоянии. А продолжить было бы неплохо. Но обо всём по порядку.
У боуденовской трубки есть масса недостатков. Это и трение пластика о трубку (я уже писал, что если пластик мягкий — его пружинистость увеличивает трение так, что при определённых условиях начинаются отстрелы). Но главное — это проблемы с ретрактами. И чем более пружинистый пластик, тем сложнее эти проблемы победить. Слишком сильно надо его вытягивать, чтобы ослабить пружину. В результате, получаем наплывы в области ретракта.
Но прогресс не стоит на месте. Ещё год назад в блоге была статья про экструдер с тонким шаговым двигателем. Правда, цена у него была, как треть всего моего принтера (вместе со штатным экструдером).
И вот сидели мы с китайским знакомым, обсуждали 3D строение. Я ему рассказал про тот моторчик. Ему стало интересно. Нашли мы тот моторчик на TaoBao. А ещё он сказал, что там полно клонов E3D Titan по смешным ценам. Стали глядеть — опа! А продаётся полный комплект. Этот мотор и экструдер по совсем неприличной цене.
В целом, на Ali Express цена за комплект тоже не запредельная. Вот первый попавшийся вариант https://ru.aliexpress.com/item/3D-Printer-Titan-Extruder-Full-Kit-with-NEMA-17-Stepper-Motor-ssupport-both-Direct-Drive
В общем, привёз я парочку таких комплектов из Китая, и стали мы с товарищем думать, как нам на свои Дельты это дело приладить. Первое время пытались найти готовые решения на thingiverse. Увы. Решений — два. Первое — на магнитах. Я бы купил магниты, но всё, что есть в продаже — там шары ставятся на диагонали, а в том решении — шары стоят на эффекторе. Поэтому пришлось отбросить. Второе решение я даже распечатал для примерки.
Во-первых, все отверстия оказались не соосны. Ни скоба не надевалась на основание, ни двигатель с экструдером не крепились к скобе. Но это — не самое страшное. Главное — расстояния между диагоналями не соответствовали моему принтеру (у меня — 40 мм). Так что это решение я просто повертел в руках, чтобы взять из него всё лучшее и не брать всё неудачное. Например, мне не понравилось, что тут во главе угла стоит центровка сопла. Как следствие, экструдер с мотором сдвинуты. Поэтому они будут мешать диагоналям, а чтобы этого не произошло — увеличен радиус эффектора. Вот тут сдвиг виден
Кроме того, единогласно (напомню, мы занимались разработкой вдвоём) было принято решене, что наш эффектор будет монолитным.
Итак. Начинаем проектирование. Я рассказываю ход мысли, чтобы кто-то увидел слабое место и спроектировал вариант, лишённый такового (и выложил, разумеется :-). В рассмотренном готовом варианте экструдер поднят над эффектором. И не ясно, как в радиатору крепить готовую систему обдува. А я уже описывал, что у меня была найдена замечательная вещь на thingiverse, Разрабатывать свою — совершенно не хотелось. Поэтому не менее единогласно было решено сделать силовое кольцо (прямо как в модельке, которую повертели в руках), а экструдер — утопить вниз, чтобы радиатор просто торчал из него. С точки зрения надевания системы обдува — отличное решение. С точки зрения радиуса эффектора — спорно. Если чуть повернуть систему, то можно выиграть несколько миллиметров, но поворачивать нельзя, так как пропадёт жёсткость. Тем не менее, вот результаты первой примерки
В целом, неплохо, но радиус эффектора был просто безобразным. А чем больше радиус эффектора, тем меньше радиус печатной зоны. Поэтому было решено повернуть крепления вверх (на фото выше они идут в бока). В результате, радиус кольца стал безобразно мал. Но это безобразие имеет смысл только когда всё собираешь в кучу, то есть, единожды. Зато потом — печатная область более-менее большая. Тем не менее, закрыть крышку эуструдера (ту самую, прозрачную) стало невозможно. Чтобы закрепить его, пришлось просверлить в нём технологическое отверстие
А чтобы систему «экструдер-двигатель» можно было опустить вертикально, было разомкнуто кольцо в скобе. Всё равно там всё держится на двигателе, так что прочность от этого не пострадала. Начинаем печатать из Керамо — отрыв от стола. Ещё раз — снова отрыв! Пришлось делать утепляющую юрту
Получилась вот такая симпатяга
Керамо — это такой пластик, где поддержки легко ломаются, а что не нравится — легко шкурится. Дальше идёт примерка на принтер. Для крепления, как оказалось, надо использовать винты M4x25. В «прошивке» следует поменять параметр DELTA_EFFECTOR_OFFSET вот так:
// Horizontal offset of the universal joints on the end effector.
#define DELTA_EFFECTOR_OFFSET 36.497 // mm
Также я уменьшил печатный радиус со 120 до 110 мм. Это — главная беда разработки. Но мы — не профессиональные конструктора. Сделали, как смогли. Если кто-то сделает эффектор меньшего радиуса — будет здорово.
Теперь — датчик BLTOUCH. Вот из этой картинки получается, что от его крепления до стола должно быть 36.3 + 8 = 44.3 мм. А у меня с моим хотэндом получилось от низа эффектора до стола 47 мм. То есть, надо было добавить пластину всего лишь на 3 мм. И все типовые решения, где в пластину вставляются гайки — идут лесом. Нет, это было бы возможно, если бы мы проводили сквозное проектирование, но тратить ещё день и ещё много метров пластика ради этого — не хотелось. Поэтому была сделана пластинка, куда были положены винты с потайной головкой. Это дело было обильно залито эпоксидкой (чтобы винты приклеились наверняка) и приклеено к эффектору снизу
А гайки привинчиваются — снизу. Ключом орудовать ужасно неудобно, но один раз — можно потерпеть.
Затем — делаем калибровку командой G33, про которую я уже писал в отдельной статье. Перед калибровкой можно также задать меньший радиус стола
M665 R155.47
Высота — зависит от положения эндстопов. У меня получилось (взято с запасом)
M665 h430
Дальше — калибровка
G29
G33
Результаты калибровки сохраняем командой
M500
Теперь надо перенастроить шаг экструдера, чтобы учесть редкутор. Глядя в перечень команд и документацию на фирменный экструдер E3D Titan, получаем такую конструкцию:
M92 E418.5
и, как всегда, сохраняем
M500
Пока почта доставляет заказанную фторопластовую трубку с внутренним диаметром 3 мм, чтобы с катушки не слетали петли, пропускаем пластик через верх
Пока версталась статья, приехала трубка. Но мне уже так понравилось текущее решение, а все пути установки полноценной трубки были так неудобны, что я пока засунул её в стол. Правда, несколько сантиметров в экструдер всё-таки нужно запихнуть, иначе пластик очень сложно вставлять, а трубка — она является направляющей для верной заправки…
И теперь печатаем крокодила, куда ж без него
Честно говоря, я не очень хочу вставлять много фотографий того крокодила. Просто я только-только научился снимать а боковом свете. Боюсь отпугнуть читателей от методики. Вот как-то так получилось на самом красивом снимке
Дело в том, что всё познаётся в сравнении. Эта Дельта по ряду причин и до абдейта почти так же слои гнула. Вот такой вышел жёлтенький крокодил
Короче, НЧ звон предсказуемо увеличился. Но динамические ускорения позволяют его привести в приемлемые пределы, не сильно потеряв скорость общей печати. Чего меня сильно тревожит — я надеялся, что вот такие прыщики
уйдут вместе с трубкой. Не ушли. Не ясно пока, как с ними бороться.
А так — с чем я больше всего хотел расстаться, с тем расстаться уже удалось. Вот этот ужас на ровном месте (пластик — очень мягкий Прототайпер)
удалось довести до почти незаметного состояния (к сожалению, напечатано не фотогеничным прозрачным прототайпером, так что фото не приводится).
Китайская промышленность освоила выпуск дешёвых пластиковых экструдеров с редуктором, а также — лёгких шаговых двигателей, что позволяет разместить систему «экструдер-двигатель» на эффекторе 3D принтера с системой «Дельта»
В ходе эксперимента был разработан эффектор, позволяющий проверить эффективность такой замены
В результате, проблемы ретракта сошли на нет, но уменьшилась область печати, а также несколько возрос НЧ-звон на моделях. Прочих проблем — пока не выявлено.
Авторы прекращают опыты в данном направлении по причине усталости от темы, но будут очень рады, если со временем появится модель эффектора, который разработан под впечатлением данной статьи, но имеет меньший радиус (что добавит радиуса печатной области).
STL модели можно скачать с нашего сайта:
С уважением В.Ш.
yes3d.ru